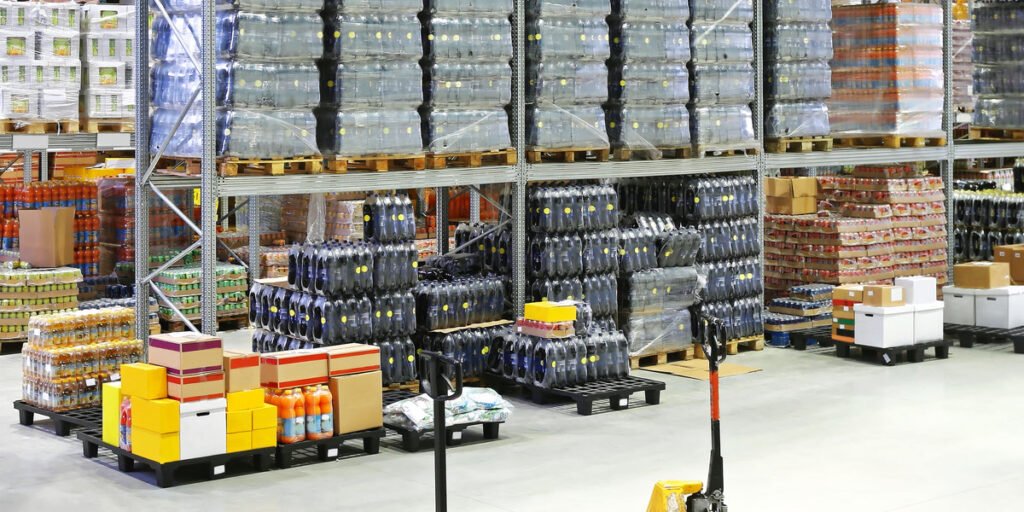
A well-organized warehouse is essential for efficient operations, and selecting the right pallet racking system is crucial in optimizing space and workflow. With various racking options available, choosing the right one can be challenging. This guide will help you understand the different pallet racking systems and how to select the best fit for your warehouse needs.
Understanding Pallet Racking Systems
Pallet racking systems are storage solutions designed to hold materials on pallets, improving warehouse organization and accessibility. They come in various styles, each offering unique benefits depending on the type of inventory, warehouse size, and retrieval requirements. The right system maximizes space, enhances productivity, and ensures warehouse safety.
Types of Pallet Racking Systems
Several types of pallet racking systems are available, each designed for specific storage needs. Choosing the right one depends on your inventory turnover, space availability, and handling equipment.
Selective Pallet Racking
Selective pallet racking is the most common type, providing direct access to all pallets. It is ideal for warehouses with high SKU diversity and frequent stock rotation. This system offers flexibility and is compatible with most forklifts, making it a cost-effective choice for many industries.
Drive-In and Drive-Through Racking
Drive-in and drive-through racking systems allow forklifts to enter the rack structure to store and retrieve pallets. Drive-in racking follows a last-in, first-out (LIFO) method, while drive-through racking follows a first-in, first-out (FIFO) approach. These systems are ideal for bulk storage of similar products with minimal SKU variation.
Push Back Racking
Push back racking is a high-density storage solution where pallets are loaded from the front and pushed back as new ones are added. It follows a LIFO storage method and is suitable for warehouses that need efficient space utilization while maintaining quick access to stock.
Pallet Flow Racking
Pallet flow racking, also known as gravity flow racking, uses a FIFO method. Pallets are loaded from the back and move forward on roller conveyors. This system is perfect for high-turnover products, ensuring seamless inventory movement and reducing handling time.
Cantilever Racking
Cantilever racking is designed for storing long or bulky items such as lumber, pipes, and steel bars. It features arms extending from a central column, allowing easy access and organization of non-standard-sized products.
Double-Deep Racking
Double-deep racking involves placing pallets two deep instead of one, increasing storage density. While it reduces direct access to every pallet, it optimizes space for warehouses handling large quantities of the same product.
Factors to Consider When Choosing a Pallet Racking System
Selecting the right pallet racking system requires evaluating various factors to ensure it aligns with your warehouse’s needs and operational goals.
Space and Layout
Assessing your warehouse’s floor space and ceiling height is crucial in determining the most suitable racking system. High-density racking solutions maximize vertical space, while wide-aisle configurations prioritize accessibility.
Inventory Characteristics
Consider the type, size, weight, and turnover rate of your inventory. Perishable goods may require FIFO storage, while bulk storage works best with LIFO systems like drive-in racking.
Accessibility and Retrieval Speed
Warehouse operations that require fast stock rotation benefit from selective and pallet flow racking. If maximizing space is the priority, high-density solutions like push back or double-deep racking may be more suitable.
Forklift Compatibility
Ensure that the chosen racking system aligns with the type of forklifts used in your warehouse. Some systems, such as double-deep or drive-in racking, require specialized equipment for efficient pallet retrieval.
Load Capacity and Safety
Pallet racking must be designed to handle the weight of stored goods safely. Overloading racks can lead to structural damage and safety hazards. Conducting regular inspections and adhering to load capacity guidelines is essential.
Benefits of an Efficient Pallet Racking System
Implementing the right pallet racking system enhances warehouse efficiency, leading to several benefits:
- Optimized Space Utilization: Maximizing vertical and horizontal space reduces storage costs and improves workflow.
- Improved Inventory Management: Organized storage enables better tracking and faster retrieval of goods.
- Enhanced Workplace Safety: Properly installed racking systems minimize the risk of accidents and equipment damage.
- Increased Productivity: Streamlined warehouse operations reduce handling time and improve order fulfillment speed.
Efficient Freight Forwarder Services for Seamless Shipping
Freight forwarder services streamline international shipping by managing logistics, customs, and transportation. These experts ensure timely delivery, handle documentation, and optimize shipping routes. Businesses benefit from reduced complexities and cost-effective solutions, enabling smooth global trade. Choose a reliable freight forwarder to simplify your shipping process and enhance operational efficiency.
Conclusion
Choosing the right pallet racking system for your warehouse depends on multiple factors, including storage needs, space constraints, and operational priorities. By understanding the different racking options and evaluating your warehouse requirements, you can select a system that improves efficiency, enhances safety, and supports business growth. Investing in the right racking solution ensures long-term benefits and a more productive warehouse environment.